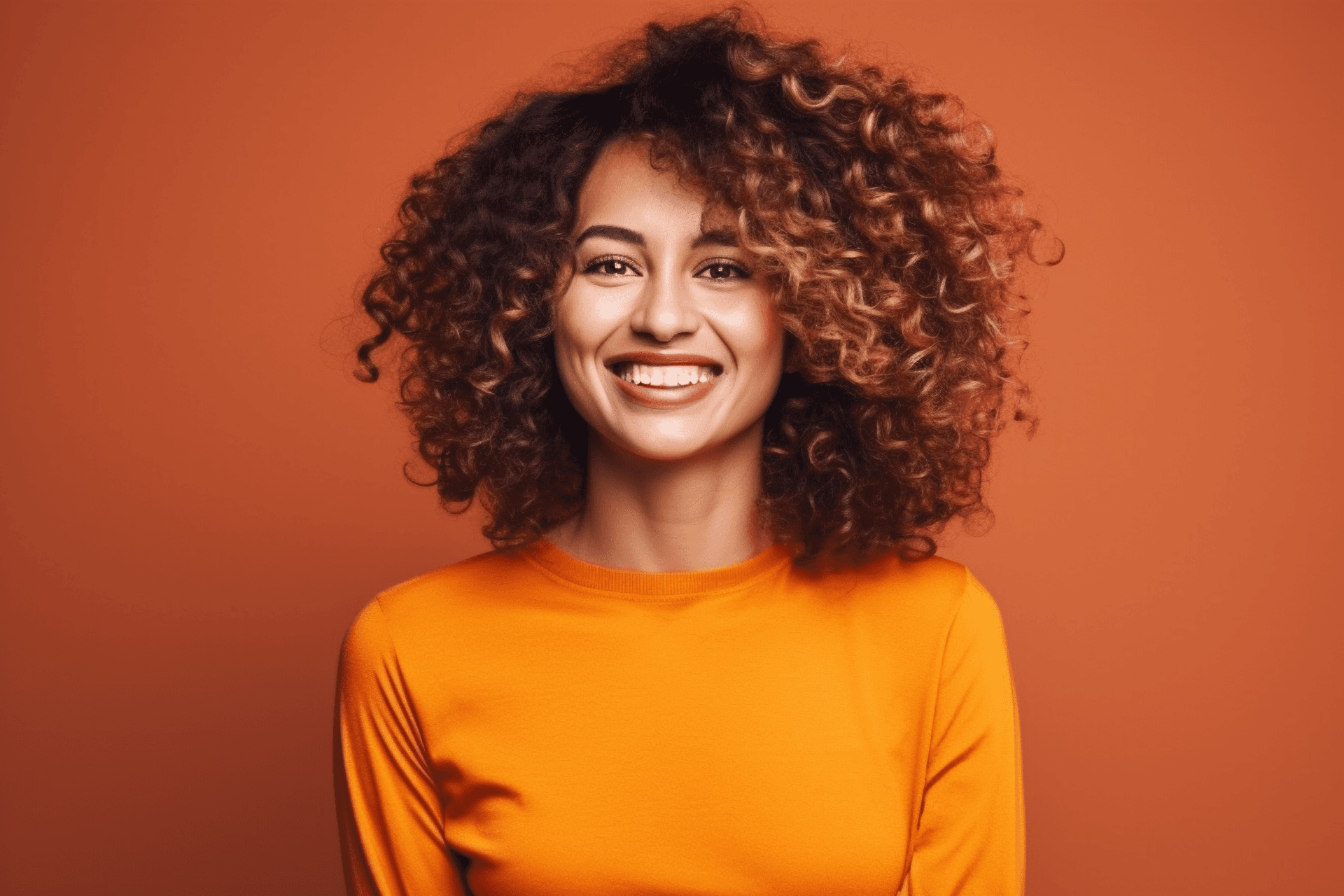
Introduction
In the cement industry, the 28-day compressive strength of cement is a critical quality benchmark. Traditionally, this parameter is assessed weeks after production, leading to reactive measures that can result in inefficiencies and increased costs. The challenge lies in predicting this strength during the production process to enable proactive adjustments. Achieving this requires sophisticated data analysis capabilities that can process vast amounts of real-time data and provide actionable insights.
The Challenge of Delayed Strength Assessment
Cement manufacturers often rely on post-production testing to determine compressive strength, which introduces a lag in quality assessment. This delay can lead to:
Overcompensation: To ensure compliance, manufacturers may use excess raw materials, increasing production costs.
Waste Generation: Inability to detect deviations promptly can result in large batches of substandard products.
Inefficient Processes: Lack of real-time feedback hampers the ability to optimize production parameters dynamically.
Essential Data Analysis Features for Real-Time Strength Prediction
To overcome these challenges, cement manufacturers need to integrate advanced data analysis features into their operations:
Real-Time Data Acquisition: Implementing sensors and IoT devices to collect data on variables such as temperature, pressure, and material composition during production.
Advanced Analytics and Machine Learning: Utilizing algorithms that can analyze historical and real-time data to identify patterns and predict outcomes, such as the 28-day compressive strength.
Predictive Modeling: Developing models that can forecast the impact of process variations on product quality, enabling proactive adjustments.
User-Friendly Dashboards: Creating interfaces that present complex data in an accessible format, allowing operators to make informed decisions quickly.
Automated Alerts and Recommendations: Setting up systems that notify personnel of potential issues and suggest corrective actions before deviations affect product quality.
Benefits of Implementing Advanced Data Analysis
Integrating these features into cement manufacturing processes offers several advantages:
Enhanced Quality Control: Real-time insights allow for immediate adjustments, ensuring consistent product quality.
Reduced Waste: Early detection of anomalies minimizes the production of substandard batches.
Cost Savings: Optimizing material usage and reducing rework leads to significant cost reductions.
Increased Efficiency: Streamlined processes and proactive maintenance improve overall operational efficiency.
Conclusion
Predicting the 28-day compressive strength of cement during production is no longer a distant goal but an achievable reality with the right data analysis tools. By embracing real-time data acquisition, advanced analytics, and predictive modeling, cement manufacturers can transform their operations, ensuring higher quality products, reduced waste, and improved profitability.
Call to Action
Interested in revolutionizing your cement manufacturing process through advanced data analysis? Contact us to learn how our solutions can help you achieve real-time quality predictions and operational excellence.
Blogs & Resources
Read our latest Blogs & resources